DSM Moves Forward in Making Electric Mobility Safer, Lighter and More Sustainable
The company has taken an important step by expanding its comparative tracking index test lab to meet next generation, high-voltage customer requirements.
DSM Engineering Materials has taken the next important action on its journey to making electric vehicles safer, lighter and more sustainable by expanding its comparative tracking index (CTI) test laboratory to meet the next-generation, high voltage customer requirements. It builds on a long track record of working with automotive tiers and OEMs, and leverages its leadership position on sustainability as well as its strong credentials in the automotive, electrical and electronics industries.
The installation of what is said to be the industry’s most advanced CTI test capabilities, is now enabling a new standard to support manufacturers in increasing the voltage of EV batteries safely and shortening charging times even further to help accelerate the shift to electric mobility. Shortening these charging times requires higher battery voltages up to 1,000V or above. To enable this ultra-fast charging at the right safety and reliability levels, manufacturers will need to use insulation plastics with better resistance to high voltages.
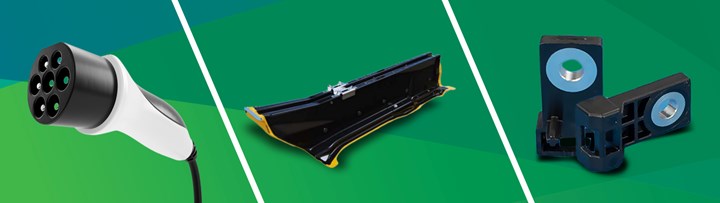
DSM Engineering Materials has already established portfolio and approach to make electric vehicles safer, lighter, and more sustainable:
▪ Safety: Leveraging its expertise in critical applications, DSM is ensuring that key future mobility systems – like the e-powertrain, connectivity, tanks and structural parts – are made with the most reliable, material solutions that meet or exceed application standards while at the same time reducing the carbon footprint of the component.
▪ Lightweighting: DSM has extensive expertise making structural parts, including actuation systems and seating materials, lighter with ForTii 4T PPA and Akulon nylons 6 and 66, said to offer best-in-class strength and thermal performance for metal replacement.
▪ Sustainability: As a sustainability leader, DSM has communicated its bold ambition to reduce its total greenhouse gas emissions and the carbon footprint of its products by 50% by 2030, from a 2016 baseline, and developing and rolling out bio- and/or recycled-based alternatives for its entire portfolio by 2030. Specific grades are already available for all major product lines.
In line with its EV-focused automotive strategy, DSM now has expanded its CTI test laboratory with equipment to validate tracking resistance to voltages up to 1,500V AC and 1,000V DC. High-voltage component manufacturers have shown significant interest in collaborating with DSM on this testing for voltages between 600 and 1,500V.
Said Franz Janson, principal product development engineer, PEE Global Automotive Resin Material Platform at TE Connectivity*, one of the world’s largest connector manufacturers, “We are very happy to see that DSM is investing in strong materials as well as the right test laboratory. We look forward to cooperating more closely to understand the impact of high-voltage exposure on material properties and to implement suitable materials for our next-generation high-voltage systems.”
*TE Connectivity is a trademark licensed by the TE Connectivity Ltd. family of companies.
Related Content
-
The Effects of Stress on Polymers
Previously we have discussed the effects of temperature and time on the long-term behavior of polymers. Now let's take a look at stress.
-
Melt Flow Rate Testing–Part 1
Though often criticized, MFR is a very good gauge of the relative average molecular weight of the polymer. Since molecular weight (MW) is the driving force behind performance in polymers, it turns out to be a very useful number.
-
Understanding Strain-Rate Sensitivity In Polymers
Material behavior is fundamentally determined by the equivalence of time and temperature. But that principle tends to be lost on processors and designers. Here’s some guidance.