Lanxess Launches Hollow-Profile Hybrid Technology
Metallic hollow profiles can be functionalized on conventional injection molding machines with plastic compounds.
A hollow-profile hybrid technology that enables metallic hollow profiles to be functionalized on conventional injection molding machines with thermoplastic compounds is now being launched by Lanxess. The new lightweight technology has been shown to result in plastic-metal composite components that boast far greater torsional stiffness and strength than could previously be achieved with other technologies for functionalizing hollow profiles. The potential applications in the automotive industry include cross car beams, coupling rods, stabilizers and seat elements. Also, this technology could be used to produce skiing and hiking poles and components for furniture and the construction industry.
Said Matthias Theunissen, an expert in lightweight design at Lanxess, “Hollow-profile hybrid technology has now progressed to such an advanced level that we have embarked on a variety of development projects with customers and have already reached the prototype stage with some of them.
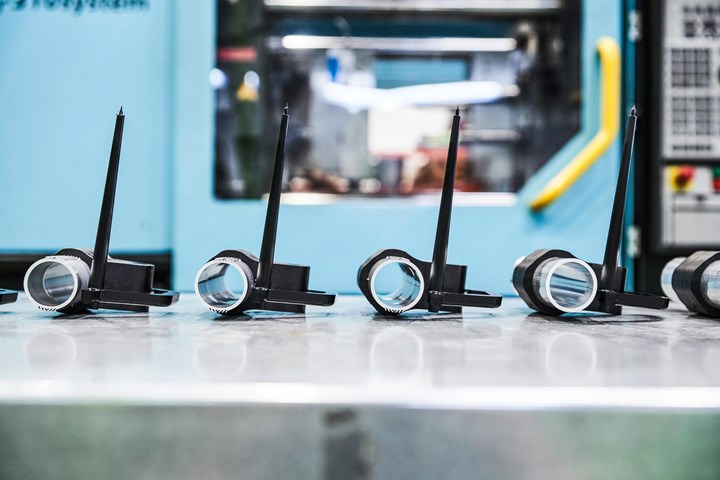
The hollow-profile hybrid technology is a further development of the “traditional” plastic-metal composite technology (hybrid technology) using sheet metal. The general strength of the new technology is that processors can manufacture with short cycle times, as is typical for injection molding in high-volume production. As a result, the manufacturing process is efficient and economical. There is no need for auxiliary units or tooling technology, which keeps investment costs low. The fact that reasonably priced hollow profiles with relatively large dimensional variations can be used helps to make the process cost-effective, too.
Explained Theunissen, “With the aid of innovative tolerance management, we can prevent profiles of that type from damaging the mold or stop leaks occurring in the injection molding cavity.” When the thin-walled hollow profiles are overmolded with the molten plastic, high pressures often exceeding 400 to 500 bar occur in the cavity. As a result, there is a high risk of the profiles deforming or collapsing. Lanxess has optimized the process so that the profiles withstand the pressures that occur and do not need to be supported from inside, according to Theunissen.
For the hollow-profile hybrid technology, Lanxess offers highly reinforced nylon 6 types such as the easy-flowing Durethan BKV60H2.0EF DUS060 with a 60% short glass fiber content. With their high strength and stiffness, these compounds further enhance the performance of the corresponding components. In a simulation study, Lanxess examined how using the compounds pays off in the design of an automotive cross car beam. According to Theunissen, the component can be designed with about 30% lower weight than an all-steel structure while offering better mechanical performance in some respects.
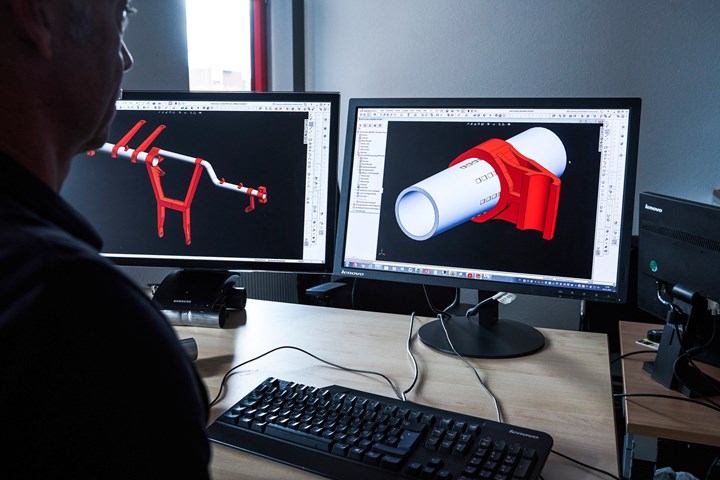
Typical load cases and component properties were calculated, such as vibration behavior and the stiffness of the steering wheel in the direction of gravitational forces. “The component also underlines the huge potential of the technology in implementing cost-saving functional integration. For example, connections for the A-pillar as well as mountings for the steering column, dashboard, climate control units and airbags were directly injected, said Theunissen.
Lanxess has developed new calculation models for the hollow-profile hybrid technology based on simulation tools that have proven successful for years in conjunction with the “traditional” hybrid technology. They reportedly allow precise prediction of the production process and the quality of the connection between the metal and plastic. For example, they can accurately predict the maximum stresses hollow-profile hybrids will withstand and at what point they will fail. “We apply this expertise in working with our customers,” explained Theunissen. A newly developed test specimen was used to validate the simulation. Extensive component testing for static and dynamic load cases underpinning the simulation results was carried out on real components.
Related Content
Getting Charged Up About Electric Vehicles
Metal-to-plastics replacement stories are a classic of the genre for plastics publishing, and nowhere more so than in the automotive space.
Read MoreDesign Optimization Software Finds Weight-Saving Solutions Outside the Traditional Realm
Resin supplier Celanese turned to startup Rafinex and its Möbius software to optimize the design for an engine bracket, ultimately reducing weight by 25% while maintaining mechanical performance and function.
Read MoreABC Technologies to Acquire Windsor Mold Group Technologies
The Tier One automotive supplier with compounding and blowmolding machine capabilities adds the 50-yr-old molder and moldmaker.
Read MoreAutomotive Awards Highlight ‘Firsts,’ Emerging Technologies
Annual SPE event recognizes sustainability as a major theme.
Read MoreRead Next
People 4.0 – How to Get Buy-In from Your Staff for Industry 4.0 Systems
Implementing a production monitoring system as the foundation of a ‘smart factory’ is about integrating people with new technology as much as it is about integrating machines and computers. Here are tips from a company that has gone through the process.
Read MoreLead the Conversation, Change the Conversation
Coverage of single-use plastics can be both misleading and demoralizing. Here are 10 tips for changing the perception of the plastics industry at your company and in your community.
Read MoreWhy (and What) You Need to Dry
Other than polyolefins, almost every other polymer exhibits some level of polarity and therefore can absorb a certain amount of moisture from the atmosphere. Here’s a look at some of these materials, and what needs to be done to dry them.
Read More